On a table at the front of the Makerspace sits a sprawl of disfigured shapes of varying colours. Behind them, a series of detailed info-graphics. Just a few days earlier, these models buckled under immense pressure when they were crush tested. The lines on the graphs illustrate when these moments occured.
Now, some of the models are nearly unrecognisable from their previous forms. Others had exploded in a maelstrom of plastic shrapnel.
However, a few of the shapes had maintained their integrity through the aggressive testing with minimal warping. For the researchers who ran these crush tests, this was an unexpected result with exciting implications.
The Makerspace hosted an innovative workshop on March 6 that focused on the results of pressure testing 3D printed PLA plastics. The results were displayed through printed models and charted data that elaborated the team’s findings from the first documented test on the strength-to-weight ratio of PLA that has ever been performed.
This offers up new insights and possible future applications of the substance.
A group of students from the civil engineering technology program, comprised of Derek Risk, Cam Huxter, Chance Hainer and Stefan Pecile, cultivated this advanced research project using a quantitative crush test to tackle the unknowns of PLA’s durability and to further our understanding of the material’s potential.
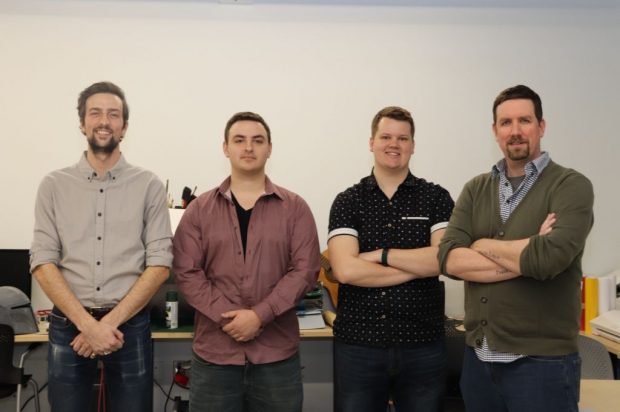
For context, PLA (polylactic acid) is a corn-based plastic which is completely biodegradable. “We specifically chose to use a corn-base plastic because it’s biodegradable,” said Stephen Gagné, acting manager of the Makerspace. “We didn’t want to open up a Makerspace that would dump a bunch of plastic in the ocean…we wanted to make sure to do something more responsible.”
Compression testing materials is a common practice in civil engineering that’s used to assess the strength of construction materials such as concrete, steel and wood. Until now, the strength-to-weight ratio of PLA has been an unknown. However, the group’s test phase has given insight into the material’s overall strength.
“We had no idea what the strength was,” said Risk. “No one else has ever done this before. We got 44 MPa out of a solid piece of PLA.”
MPa, or megapascals, is a measure of compressive strength of a material. One MPa is equivalent to a million pascals, which is one newton of force per square metre. Usually, concrete can range from 17-28 MPa for residential and commercial construction respectively, and anything over 41 MPa is considered
“high strength” material.
Thus the 44 MPa of PLA comes as a staggering quantifiable – the catch: the material’s modulus of elasticity. Basically, the elastic modulus is a measure of a substance’s resistance to deformation under stress, which was readily displayed by the stress-strain charts presented at the event.

The tests involved several different structural PLA prints of varying degrees of durability, however the solid was determined to be the most resistant to deformity. This is where the PLA begins failing to meet standards for construction.
“It’s stronger than concrete, but it deforms quite a bit more than anything we use in construction,” said Risk. “Strong enough but not ridged enough.”
The modulus of elasticity for concrete is about 41,000 MPa, steel 200,000 MPa, a vertical pine column at 9,000 MPa, while PLA measured only 1,800 MPa.
Weather is also an issue for PLA. “It’s weak if you have it outside, it’ll degrade too quickly,” said Huxter. “But you can 3D print different design prototypes out of different materials. It’s still expensive to 3D print, but our hope is that in the future it will be more affordable.”
The viability factor second only to composition of PLA is its cost effectiveness.
“We did a feasibility study and our conclusion is that right now it’s not a useful construction material,” said Risk. “We got 3 cents a gram here… but if we can compare the price of PLA to the price of concrete, it’s 30,000 times more expensive than concrete, and that’s a big hurdle.”
Though the Makerspace is well equipped for plastics and soon to be resin based 3D printing, some printers – like the one at Algonquin’s ACCE lab – are capable of manufacturing construction materials.
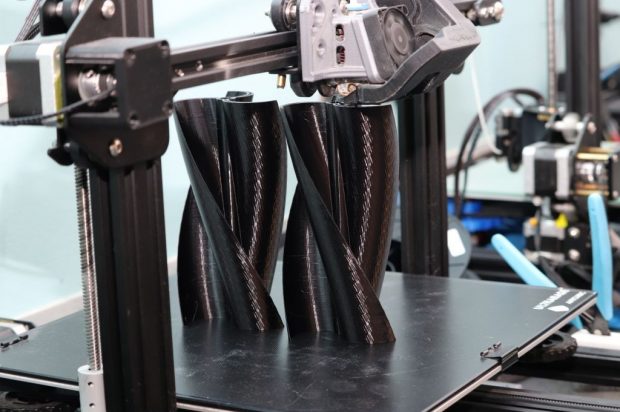
“They already 3D print concrete now, they started building houses out of it for only $10,000 so trying to beat that is hard,” said Pecile.
Despite these numbers, the team is hopeful that this discovery will promote research to be carried out by future students of the civil engineering technology program.
“Makerspace has a number now,” said Hainer. “Next year [students] could reinforce the plastics, find better plastics, covering the plastics so weather isn’t as huge a factor, also finding different uses for what we currently have. In theory, it could be used as a safety factor because it shows deformation. You could place it in a concrete pillar and be able to see deformation before a collapse. The possibilities of working with (PLAs) are endless.”
The team is required to publish their findings for the civil engineering technology program by March 7, 2020.